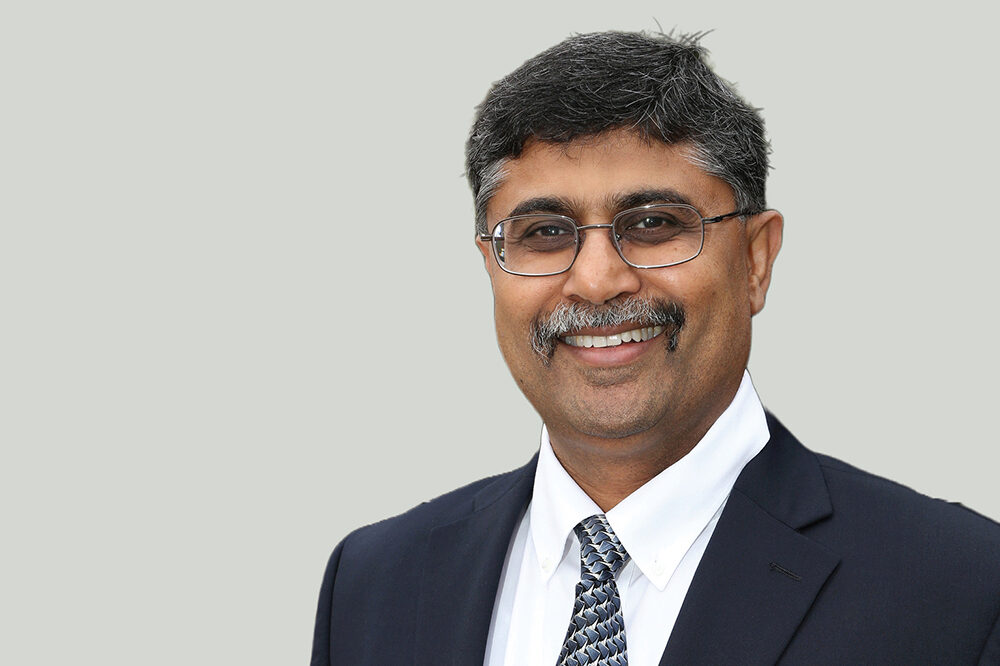
Cyber Manufacturing Research Team Awarded $3M NSF Grant
November 21, 2022
By Ian Sargent
Shreyes N. Melkote, who holds the Morris M. Bryan, Jr. Professorship in the George W. Woodruff School of Mechanical Engineering, has been awarded a $3 million Future Manufacturing Research Grant from the National Science Foundation (NSF). Melkote, who is also the Associate Director of the Georgia Tech Manufacturing Institute and Executive Director of the Novelis Innovation Hub, will act as principal investigator alongside four other researchers, including Woodruff School Professor Emeritus David Rosen, and will explore a data-driven approach to cyber manufacturing. The grant will also support Melkote’s efforts to work with academic and industry partners to develop educational tools to train a future manufacturing workforce from diverse backgrounds.
“We are excited to have the resources that the NSF has provided,” Melkote said. “It’s the best type of resource because it allows us to do basic research.”
Cyber manufacturing looks to leverage recent advances in artificial intelligence and machine learning, cloud technology and the expanding reach of the Internet-of-Things to reduce the cost and time of producing discrete parts. Presently, the manufacturing process is compartmentalized, with design, fabrication, and distribution heavily reliant on direct communication between the parties, and often involves multiple iterations of a design before the customer’s needs are met.
In a future cyber manufacturing ecosystem, the process is digitally unified across the supply chain and potential issues in fabrication can be flagged automatically and early in the design process, minimizing the need for multiple prototypes. The final design can then swiftly be routed to those best equipped to produce the product based on the specifications.
This vision of a fully automated, interconnected process has long been sought after and is considered the ‘holy grail’ of discrete parts manufacturing.
“It's an old problem,” Melkote said. “But we have new ways of potentially trying to solve it, and we have a critical mass of people and resources to help solve, or at least make a significant dent, in solving the problem.”
A crucial step in solving the problem requires digitizing and automating the complex series of decisions that begin when a new design for a product is completed. What are the manufacturing processes (and machines) required to produce the design? What processes create the most durable build, or the most cost-efficient? Can the design be altered for manufacturability without compromising functionality and quality?
For mass-produced discrete products or parts built to universal standards, these are questions to which suitable answers have been found through trial-and-error, but bespoke or new designs often require specialized knowledge about manufacturing processes and their capabilities. A company or individual will use their current level of understanding to discern how to move forward with a brand-new design.
“Fundamentally they are harnessing the knowledge derived from data they have tucked away somewhere and then using that to actually take a shot at figuring out how to make it,” Melkote explained. “But it would be great if they had all of these capabilities in an automated way. This grant is focused on how you generate the complex knowledge that individuals have acquired through experience.”
Melkote’s interdisciplinary approach will use generative machine learning and other artificial intelligence techniques to help automate this complex decision-making process. If a computer can infer the capabilities and limitations of an industrial manufacturing process and associated machines, then it should be able to make intelligent deductions about the entire manufacturing process, at least in theory. Extracting the data necessary to make this happen requires new methods that Melkote and his co-investigators will research.
“If I can teach a computer to be able to learn these things, the more data from successfully produced parts I can provide it, then its learning will improve and its ability to get close to telling me what all the types of things I can produce using a given process on a given machine will improve.”
The models and algorithms that would run this process could then be embedded in an automated cyber manufacturing service, which can analyze an uploaded design and provide a customer with instant feedback regarding recommended modifications, and projected costs, or even generate instructions and send them to the right machine. The work could see sweeping changes made to several manufacturing industries and democratize the way products are designed and made.
Alongside Rosen, Melkote will work closely with three other researchers, two of which have ties to Georgia Tech, including Matthew Gombolay, an assistant professor in the School of Interactive Computing, and Mahmoud Dinar, a former postdoctoral fellow at the Woodruff School and current Assistant Professor at California State University-Sacramento. Dr Gaurav Ameta, a research scientist at Siemens Corporate Technology will also work as co-principal investigator.
The grant is part of a wider national initiative that saw more than $30 million awarded to university-based research projects on advanced manufacturing and preparation of the manufacturing and STEM workforce for the future.