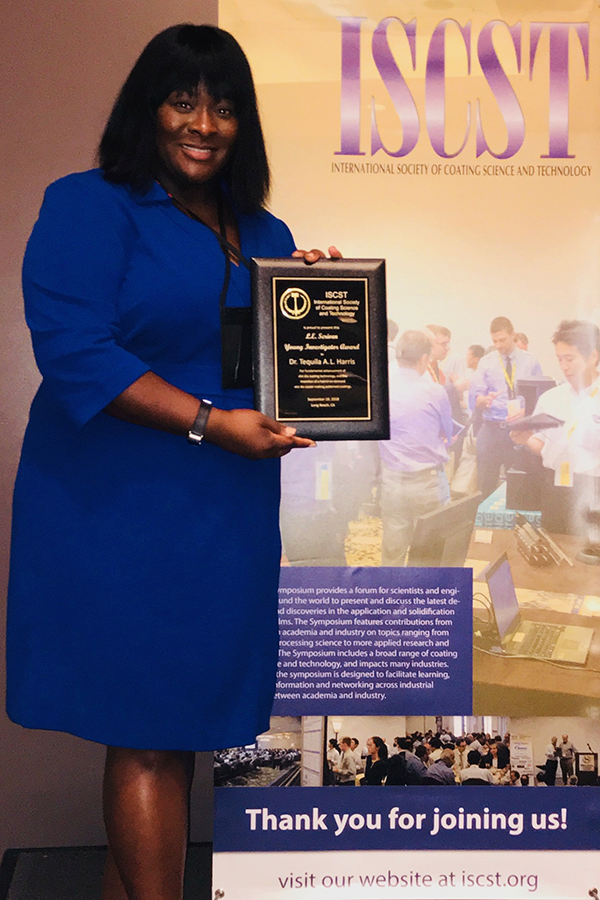
Existing high-throughput coating technologies are able to manufacture thin films in continuous single sheets but generally require a secondary etching or ablation process to pattern the coating. Emergent technologies, such as organic electronics, are compatible with these processes and can also be processed in ambient conditions, making them low cost and conducive to mass production. However, the market is currently limited to rigid slot die designs that only allow for the extrusion of lines or stripes that are the width of the shim opening. Thus, there exists a need for a high-throughput technology that can process materials with different patterns such as circles, lines, and wafers. Such a technology would have energy, environmental, and electronics applications including organic solar cells, organic LEDs, batteries, thin film transistors, radio frequency identification tags, and other devices whose manufacturing methods are currently restricted to ink jet printing and vapor deposition.
Based on a novel method of controlling flow, Dr. Harris' technology systematically integrates computer-aided design (CAD), a complex algorithm, and the tool. The advantage of this hybrid tool is that it allows for a purely additive approach to making layer-based devices without the need for an additional subtractive step. With the integration of CAD into the system, the process allows for making complex patterns that cannot be realized by other technologies. This single-step process will also allow for significant cost savings over traditional methods, especially when processed at ambient conditions.