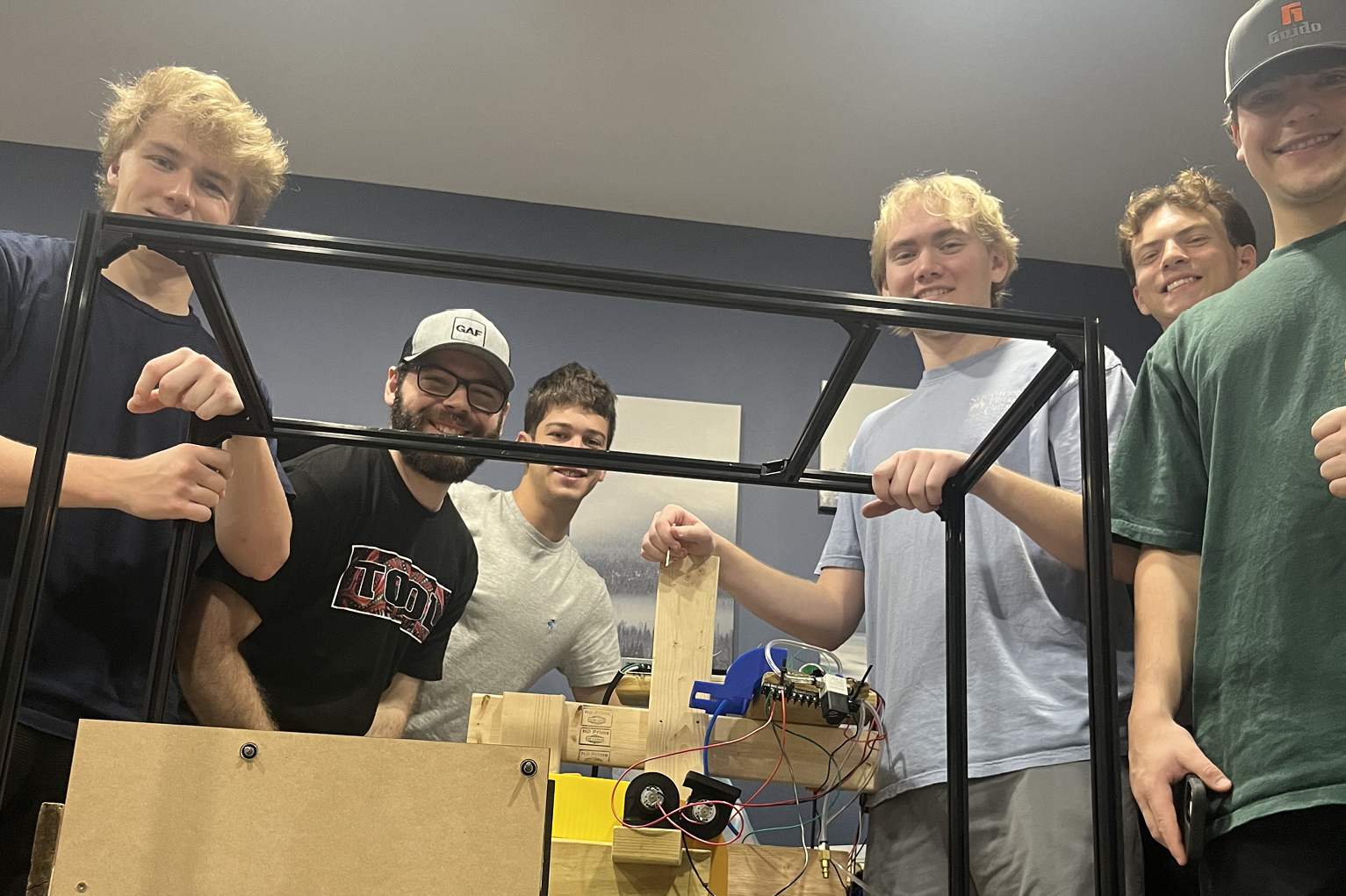
Meet Fall 2024 Capstone Design Team Megatronics
November 8, 2024
By Alba Garcia-Sarabia
Get to know mechanical engineering Capstone Design team Megatronics who is creating a fully autonomous system for Crystal S.A.S. that is able to receive, bag, label, and box socks for the Fall 2024 Georgia Tech Capstone Design Expo. The team's advisor is Professor Julie Linsey.
1. Can you tell us about your team and project?
Our team, Megatronics, has six members, each of whom are mechanical engineers. Team members include:
- Jonathan Hampton – Perry, Georgia
- Matthew Hawn – Gainesville, Georgia
- John Heyerdahl – Alpharetta, Georgia
- Evan Rodgers – Atlanta, Georgia
- Avery Skolnick – Bedford Hills, New York
- Coleman Thompson – Atlanta, Georgia
Our team is divided into three subteams: electrical, CAD, and prototype. Our group is working with Crystal AG to design an automated sock packaging system. Crystal AG is a manufacturer that works with companies such as Lululemon and ALO to manufacture all kinds of clothing products. The goal of the project is to double the throughput of socks to at least 15 pairs per minute with a budget of $5,000, about a tenth of comparable industry products. Additional constraints include not being able to use heat for any part of the process such as sealing the bags, and the bags must be recyclable.
2. What is your team’s design process, how do you go about separating different tasks, and what are some of the biggest challenges you have faced?
Most of our team’s design process was done iteratively by designing, then prototyping and then redesigning with knowledge gained from prototyping. As forces and distances for this project are extremely small, minor vibrations or wrinkles in the sock had large effects on the functionality of the system. Due to this variance, hand calculations alone were insufficient for designing the product.
Tasks were separated by what members had experience working with in the past. Although we are all mechanical engineers by major, we have very different skills sets that can be put together to form a well-rounded and functional team.
The largest problem we faced was designing the device that held the bag while it was open. We first started with a vacuum lifter which worked in theory and early testing, but in practice the seal was too inconsistent. The next iteration was just a roller on the top of the slide with the idea the bag would go under the roller normally. This iteration failed to work as the bag would go over the roller and the roller had a tolerance of less than a width of electrical tape. The next design added a second roller underneath the first roller to remove the friction of the top roller and with the idea the second roller would be softer than the slide component and increase the tolerance. This design worked when the bag was guided between the rollers by something on top, but without that the bag would get jammed. The fifth and final iteration features a guide over the rollers with two rollers. One roller is powered, and the other roller isn’t. The two rollers are in contact but touching slightly so that the bags can be fed through them by the bag dispensing system.
3. Have there been any highlights while working on your project?
The highlights of working on the project have been the group work sessions. Whether in the design or prototyping sections, when the team comes together it is always very productive and a lot of fun.
4. Can you tell us about your experience working with a sponsor?
Our sponsor, Crystal S.A.S., has been a pleasure to work with. Our point of contact, Juan, is extremely responsive and a huge help to the project. He has been ready to support us throughout the semester and gives constructive feedback.
5. If you could go back in time, what advice or message would you give your team on day one?
The biggest advice we would give ourselves is to prototype sooner. Our project was extremely hard when it came to prototyping, with parts that took approximately 10 hours to print. Every time we needed to replace a part it took a day to re-cad and then a day to print. If we had been able to start prototyping sooner, we could have iterated through designs sooner and could have had more time to improve the system from a functional and aesthetic stance.
The Fall 2024 Georgia Tech Capstone Design Expo will be held on Monday, December 2, at McCamish Pavilion on the Georgia Tech campus. At the Expo, over 600 seniors from various disciplines of engineering and industrial design will showcase their innovative projects designed and built during their Senior/Capstone Design course. Register to attend here!
This semester's Expo includes various industry sponsors whose donations support Transforming Tomorrow: The Campaign for Georgia Tech.