Education
- Ph.D., Rensselaer Polytechnic Institute, 2006
- M.S., Rensselaer Polytechnic Institute, 2003
- B.S., Lane College, 2000
Background
Began at Tech in October 2006 as an Assistant Professor.
Research
- Manufacturing and Fluid Mechanics; Polymer processing, mechanical system design, fluid flow, and mechanical and physical property characterization of thin film.
Dr. Harris’ research is focused on exploring the connectivity between the functionality of nano- to macro- level films, components, and systems based on their manufacture or design and their life expectancy, thereby elucidating mechanisms by which performance or durability can be predicted. She is interested in using both simulations and experimentation to better understand this connectivity.
By addressing complex fundamental problems, Dr. Harris aims to impact a plethora of industries, although applications of direct interest to her include energy (e.g., polymer electrolyte membrane fuel cells), electronics (e.g., organic electronics), and environmental (e.g., water).
She has experience in developing systematic design and manufacturing methodologies for complex energy systems which directly involve material characterization, tooling design and analysis, computational and analytical modeling, experimentation, and system optimization. Currently her research projects focus on investigating the fundamental science associated with fluid transport, materials processing and design issues for energy/electronic/environmental systems. Problems of interest include:
(1) Understanding the influence of transport properties on initiation and propagation of defects in thin film materials as they are manufactured. From this work an understanding of how manufacturing leads to premature degradation and failure of polymer membrane thin film, through experimental analysis and numerical analysis will be elucidated, which is especially important for separation media. The upper and lower processing window, as shown in Figure 1., and an empirical model to cast relatively high viscosity solutions have been developed. [See refs. 5,2,1 below]
(2) Investigating the fluid flow characteristics through porous media of various designs and shapes. Direct coating of solution onto a porous substrate, as shown in Figures 2., is not trivial due to various wetting phenomena. Although, the ability to directly coat a porous substrate has major advantages, such as reduced waste and reduced manufacturing time and cost. From this work a basic understanding of the mechanisms that must be controlled or of how materials must be tailored to control the suspension and adhesivity between layers will be elucidated, when directly coating viscous solutions onto a porous substrate. [see refs. 6,4,3 below]
(3) Implementing innovative thin film manufacturing techniques that allow for in–line processing of patterned materials in on step and layered materials via multiple passes. Roll-to-roll thin film processes are not traditionally used to make 2D and 3D materials. In this work, an innovative hybrid manufacturing tools will be developed and its functionality characterized based on the influence of various processing parameters. This work will allow for unique flexible thin film structures to be created at the macro scale, using one tool and minimal processing steps, which has not been realized to date.
(4) Implementing novel polymer electrolyte membrane fuel cell (PEMFC) designs and assemblies that have increased performance, decreased cost, and that are sustainable. A host of challenges continue to plague the PEMFC industry. In this work we explore DFMA methods for (a) reducing the number of components in the system, (b) redesigning components, (c) manufacturing the components or sub-assemblies, and (d) increasing production rates, thereby reducing the overall cost of PEMFC stack. In addition, it is anticipated that several durability issues will be mitigated with the implementation of innovative designs and assemblies. [See ref. 3]
![]() Figure 1. Coating window |
![]() Figure 2a. Microstructure of a |
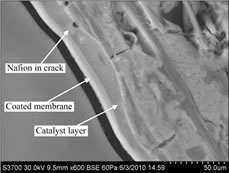
Figure 2b. Direct coating Nafion™
onto a catalyzed gas diffusion
layer. Illustration of how surface
imperfections lead to undesired
wetting effects. [see ref. (3)]
- National Science Foundation Faculty Early Career Award, 2010-2015
- Lockheed Inspirational Young Faculty Award, 2010
- National Science Foundation/Integrated Graduate Education and Research Trainee, 2005-2006
- 1969 Teaching Fellow, 2007 - 2008
- United Negro College Fund Young Alumnus Award of the Year, 2005
- Alliances for Graduate Education and the Professoriate Fellow, 2003-2004
- The Henry Luce Foundation Clare Luce Booth Fellow, 2002-2003
- General Electric Faculty of the Future Fellow, 2000-2001
Representative Publications
- Kanthi Latha Bhamidipati; Sima Didari; Prince Bedell; Tequila A. L. Harris. 2011. Wetting phenomena during processing of high-viscosity shear-thinning fluid. Journal of Non-Newtonian Fluid Mechanics, 166 (12-13) pp. 723-733.
- Bhamidipati, K.; Harris, T. 2011. Numerical Analysis of Defect Formation during Fabrication of High Temperature Polymer Electrolyte Membrane Solutions. Journal of Polymer Science and Engineering, 51(5), pp.1701-1709.
- Caston, T.; Carney, H.; Bhamidipati, K.; Harris, T. 2011. Graduated Flow Resistance to Gas Flow Through a GDL in an Unconventional PEM Stack. ASME Journal of Fuel Cell Science and Technology, 8, 011003.
- Caston, T.; Murphy, A.; Harris, T. 2010. Effect of Weave Tightness and Structure on the In-Plane and Through-Plane Air Permeability of Woven Carbon Fibers for Gas Diffusion Layers. Journal of Power Sources, 196(2) pp.709-716.
- Bhamidipati, K.; Harris, T. A. L. 2010. Numerical Simulation of a High Temperature Polymer Electrolyte Membrane Fabrication Process. ASME Journal of Fuel Cell Science and Technology, 7(6) pp. 061005-061012.
- Ding, X.; Didari, S.; Fuller, T.; Harris, T. 2010. A New Fabrication Technique to Manufacture an MEA Using Direct Coating of Nafion; onto Catalyzed GDL. Electrochemical Society Transactions, 33, #B7-0767.
- T. A. L. Harris, D. Walczyk, R. Puffer, and R. O'Donnell. 2004. Design of an Experimental Test Bed for Depositing Membrane Material for High Temperature Fuel Cells. Proceedings of the 2004 SME North American Manufacturing Research Conference, 431-438.